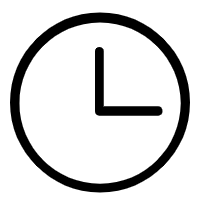
CNC vertical lathes are indispensable and important equipment in modern manufacturing, and their track types have an important impact on the performance and service life of the equipment. At present, CNC vertical lathes are mainly divided into two types: hard rail and linear rail, each with its own characteristics and applicable scenarios.
Hard rail CNC vertical lathes use steel guide rails to transmit power through sliding friction. Because the steel guide rail has high rigidity and durability, the hard rail CNC vertical lathe can withstand large cutting forces and torques, and is suitable for processing large and heavy parts. In addition, the sliding friction of the hard rail CNC vertical lathe is smaller, so the heat and frictional resistance generated are also smaller, which is beneficial to improving processing accuracy and stability.
However, hard track CNC vertical lathes also have their shortcomings. Due to the large contact surface of steel guide rails, a large amount of lubricating oil is required for lubrication, which has a certain impact on the environment and health. In addition, hard rail CNC vertical lathes require high manufacturing and installation accuracy, and maintenance costs are relatively high.
Linear CNC vertical lathes use rolling friction to transmit power and reduce friction resistance through precision balls or rollers, thereby improving movement speed and positioning accuracy. Since the contact surface of the linear CNC vertical lathe is smaller, less lubricating oil is required, which has less impact on the environment and health. In addition, the manufacturing and installation accuracy requirements of linear CNC vertical lathes are relatively low, and the maintenance costs are also low. However, linear CNC vertical lathes also have their limitations. Since the frictional resistance of rolling friction is small, high-precision balls or rollers need to be used, which increases manufacturing costs. In addition, linear CNC vertical lathes have relatively low tolerance for cutting forces and torques, and are suitable for processing small and medium-sized parts.
Choosing the track type of a CNC vertical lathe needs to be weighed based on specific needs and scenarios. If you need to withstand larger cutting forces and torques and process large or heavy parts, then the hard rail CNC vertical lathe may be more suitable; if the requirements for movement speed and positioning accuracy are higher, less lubricating oil is required, and lower manufacturing costs are required. cost, then the linear CNC vertical lathe may be more suitable.