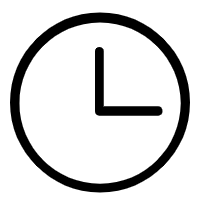
CNC lathes play an increasingly important role in modern manufacturing. However, various problems may occur during the processing, the most common of which is taper ellipse. If this problem is not solved in time, it will not only affect product quality, but may also cause serious production accidents.
There are many reasons for the taper ellipse problem of CNC lathes. The most common reason is that the spindle and the tool are not clamped correctly, which causes the tool to be unevenly stressed during the cutting process, resulting in taper. In addition, accuracy issues with the machine tool spindle and improper cutting parameter settings can also lead to the appearance of taper ellipses. To solve the taper ellipse problem, we must first start with prevention. Before processing, the clamping condition of the spindle and the tool should be checked to ensure that the clamping is upright. In addition, the machine tool spindle should be regularly inspected and maintained for accuracy to ensure that the spindle accuracy is within the allowable range.
In terms of cutting parameter settings, reasonable selection should be made based on the workpiece material, tool material and processing requirements to avoid the occurrence of taper ellipses due to improper cutting parameters. If the taper ellipse problem has occurred, appropriate remedial measures should be taken. First of all, processing should be paused to check the clamping condition of the spindle and the tool. If there are any problems, they should be adjusted in time. At the same time, you should also check whether the cutting parameter settings are reasonable and readjust them if necessary. For products that have already developed taper ellipses, they can be reworked or repaired to minimize losses.
In short, solving the taper ellipse problem that occurs in CNC lathe processing requires starting from two aspects: prevention and remedy. Precautions should be taken before processing, and the machine tool should be inspected and maintained regularly to ensure that the spindle and tool are clamped upright and the cutting parameters are set appropriately. If the taper ellipse problem has occurred, corresponding remedial measures should be taken promptly to avoid greater losses. Through the implementation of the above measures, the occurrence of taper ellipse problems can be effectively reduced and product quality and production efficiency can be improved.