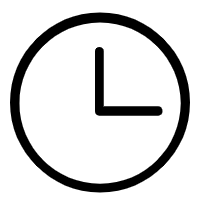
Lathe tool compensation is a key technology in CNC lathe machining, which can effectively improve machining accuracy and reduce dimensional errors caused by tool wear or replacement. By setting the tool compensation parameters reasonably, operators can ensure the consistency and accuracy of part dimensions without the need for frequent program adjustments. The following is a detailed introduction on how to use tool compensation on CNC lathes.
The basic concept of tool compensation
Tool compensation is divided into tool length compensation (TLC) and tool radius compensation (TRC). Tool length compensation is used to correct dimensional errors in the Z-axis direction caused by the difference between the actual length of the tool and the set length; And tool radius compensation is used to solve the problem of over cutting/under cutting due to tool wear, different tool radii, or contour machining.
Steps for setting tool compensation
1. Determine compensation number
Firstly, assign a unique compensation number to each tool, which is done in the tool management of the CNC system. The compensation number usually corresponds to the tool position, making it easy to manage and call.
2. Enter compensation value
In the tool parameter setting interface of the CNC system, input the length compensation value (if necessary) and radius compensation value of the tool according to the actual situation. For length compensation, it is necessary to consider the length of the handle, the length of the blade, and the possible amount of wear; The radius compensation is set based on the actual size of the tool tip arc.
3. Activate compensation function
When writing or modifying machining programs, use G codes (such as G41 and G42 to activate left and right radius compensation, G43 and G44 to activate positive and negative length compensation) to indicate when the CNC system applies these compensation values. Usually, these instructions are added to the travel path of the tool before starting cutting.
4. Real time adjustment and monitoring
During the machining process, the operator should regularly check the dimensions of the machined parts and adjust the tool compensation value in a timely manner based on the measurement results to compensate for the impact of tool wear. Modern CNC systems often have online monitoring and automatic compensation functions, which can further simplify this process.
By mastering and applying tool compensation technology proficiently, not only can machining efficiency be significantly improved, but also the machining quality of products can be ensured, and the scrap rate can be reduced. This is an indispensable part of CNC lathe operation skills.