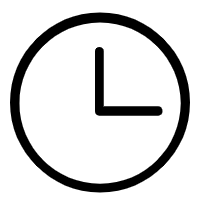
Firstly, geometric accuracy inspection of machine tools
The geometric accuracy of machine tools refers to the accuracy of the contour shape, dimensional accuracy, and positional accuracy of the workpiece during the machining process of CNC lathes. The geometric accuracy inspection of machine tools generally includes the following aspects:
1. Straightness inspection: Check the straightness of the guide rail to determine if there are any bending, expansion, or other issues with the guide rail.
2. Parallelism inspection: Check the parallelism between the guide rails to determine if they are parallel.
3. Verticality inspection: Check the verticality between the surface of the guide rail and the surface of the crossbeam to determine whether the guide rail is vertical.
4. Repetitive positioning accuracy test: Check the repetitive positioning accuracy of the machine tool, and determine whether the machine tool can repeat positioning to the extent of small machining errors.
Secondly, servo system accuracy inspection
The precision of servo system refers to the precision of servo motor, driver, encoder and other servo systems during the machining process of CNC lathe. The accuracy inspection of servo systems generally includes the following aspects:
1. Position accuracy test: Check the position accuracy of the machine tool under the control of the servo system in different motion states.
2. Repeated positioning accuracy test: Check the positioning accuracy of the machine tool under the control of the servo system when processing the same workpiece multiple times.
3. Deviation output accuracy test: Check the control error of the machine tool during the machining process under the control of the servo system.
Thirdly, machining error inspection
Processing error refers to the error generated during the reprocessing process of a CNC lathe. The inspection of processing errors generally includes the following aspects:
1. Diameter error inspection: Check the spindle diameter error of the CNC lathe, and determine the error that occurs when the CNC lathe processes workpieces with larger diameters.
2. Roundness error inspection: Check the roundness value of the workpiece processed by the CNC lathe to determine whether the workpiece meets the requirements.
3. Surface quality inspection: Check the surface quality of the workpiece processed by the CNC lathe, determine whether the surface of the processed workpiece is smooth, and whether there are defects such as scratches and burrs.
In summary, the accuracy inspection of CNC lathes is crucial, and all inspection indicators need to comply with corresponding inspection standards to ensure that the precision of the processed products meets the requirements.