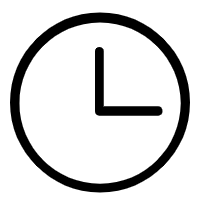
The main reasons for the temperature rise of the CNC lathe spindle are as follows:
1. Friction heat: During high-speed operation of the CNC lathe spindle, heat will be generated due to friction, causing the bearing temperature to rise. Especially when the lubrication of the spindle is poor, the friction between the spindle parts will increase, thereby generating excessive friction heat and causing the temperature to rise.
2. Cooling system failure: Cooling system problems such as CNC lathe cooler failure or pipeline blockage will cause the temperature of the lubricating oil to rise, thereby affecting the heat dissipation effect of the spindle and causing the spindle temperature to rise.
3. The spindle speed is too high: When the CNC lathe is running at high speed, the lathe spindle itself will generate a certain amount of heat. This heat generation increases when the rotational speed is too high, causing the spindle temperature to rise.
4. Processing conditions: If the tool is too old or excessively worn during CNC lathe processing, it may cause the lathe spindle to feed too much, resulting in heating.
5. Operating environment: CNC lathe spindles usually operate in complex environments. Different working conditions, such as high temperature, high humidity, high altitude or long-term low-speed operation, may cause the bearing temperature to rise.
6. Bearing material: The quality of CNC lathe bearing materials is different, and its thermal conductivity and load-bearing capacity will also be different, which will also affect the temperature rise of the bearing.
In order to reduce the temperature rise of the CNC lathe spindle, measures such as optimizing the working environment, selecting high-quality bearing materials, and ensuring the normal operation of the lubrication and cooling systems can be taken. These measures help maintain the stability and processing accuracy of CNC lathes and improve production efficiency.