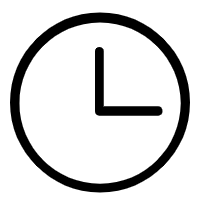
The selection and installation of precision CNC lathe turning tools are crucial to obtaining high-precision machining results. Here are some suggestions for selecting and installing turning tools:
Choice of turning tools:
1. Tool type: Select the appropriate tool type according to the material and processing requirements of the CNC lathe workpiece, including external cutters, internal cutters, turning cutters, grooving cutters, etc.
2. Tool material: Consider the hardness, machinability and other characteristics of the CNC lathe workpiece material, and select appropriate tool materials, such as carbide, high-speed steel, etc.
3. Tool tip shape: Different tool tip shapes of CNC lathes are suitable for different processing needs. Flat tips, bevel tips, radius tips, etc. are available for different types of turning and cutting operations.
4. Tool coating: Some CNC lathe cutting tools may have coatings, such as coated carbide cutting tools, which can improve the life and wear resistance of the cutting tools.
5. Tool size: According to the size and shape of the CNC lathe workpiece, select the appropriate size tool to ensure that the tool can cover the entire processing area.
Installation of turning tool:
1. Clamping system: CNC lathes use a suitable clamping system to clamp the cutting tools. This may include handles, sheaths, holders, etc. Make sure the clamping system has sufficient stability and rigidity.
2. Tool installation angle: Choosing the correct tool installation angle for CNC lathes usually depends on the type of turning or cutting. Make sure the tool is installed correctly to avoid vibration and misalignment.
3. The projected length of the tool: The CNC lathe controls the projected length of the tool to ensure that the tool does not produce excessive vibration during cutting. The choice of projection length is also related to the diameter of the tool.
4. Centering of the tool: The CNC lathe ensures that the tool is correctly aligned so that the cutting force is evenly distributed and avoids uneven cutting caused by tool deviation.
5. Tool pass amount: The CNC lathe sets the appropriate tool pass amount, that is, the distance when the tool contacts the workpiece. This helps control cutting depth and improve machining accuracy.
6. Coolant: CNC lathes use appropriate coolant to cool the tool and workpiece, while also helping to remove chips and improve cutting efficiency.
7. Positioning of the tool: The CNC lathe ensures that the tool is accurately positioned in the tool holder or tool sleeve to prevent deviation of the tool during operation.
Before installing a turning tool, it is best to refer to the CNC lathe's operating manual and manufacturer's recommendations to ensure proper installation and use. Regularly checking the wear of cutting tools and replacing them promptly is the key to maintaining machining accuracy.